How To Deal WIth Power Cable Core Breakage
- Share
- Issue Time
- Feb 1,2024
Summary
Do you know how to deal with power cable core breakage?
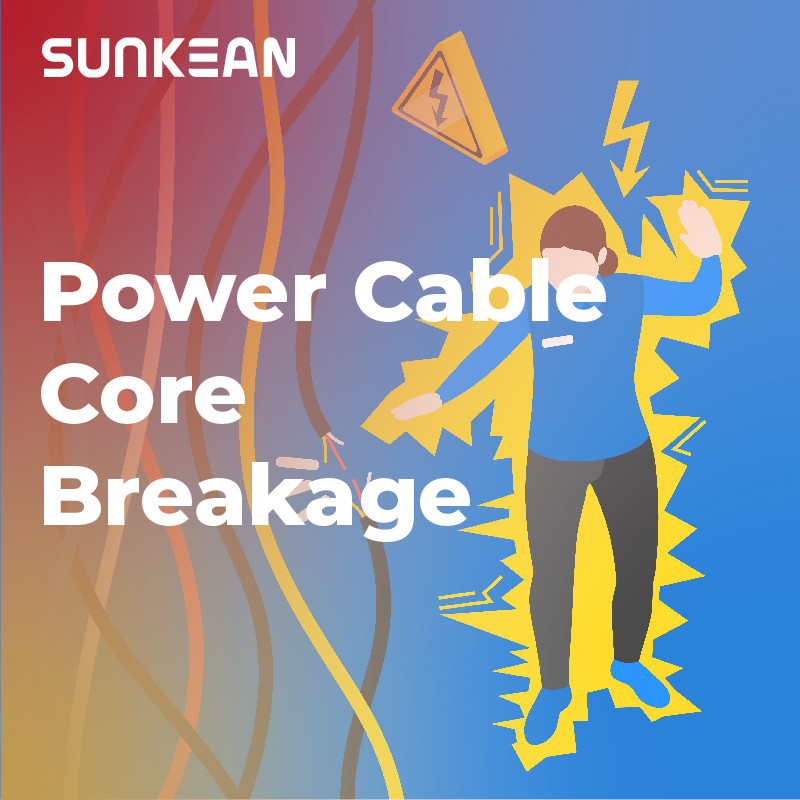
Ⅰ. Introduction
Power cables are the silent heroes of our modern world, quietly carrying electricity to power our homes, businesses, and industries. We seldom think about the intricate network of cables that weave through the ground beneath our feet or stretch across vast distances overhead. Yet, these cables are the lifelines of our electrical infrastructure, ensuring that power flows reliably and safely from its source to its destination. However, within this intricate network lies a hidden vulnerability - power cable core breakage.
Ⅱ. Understanding Power Cable Core Breakage
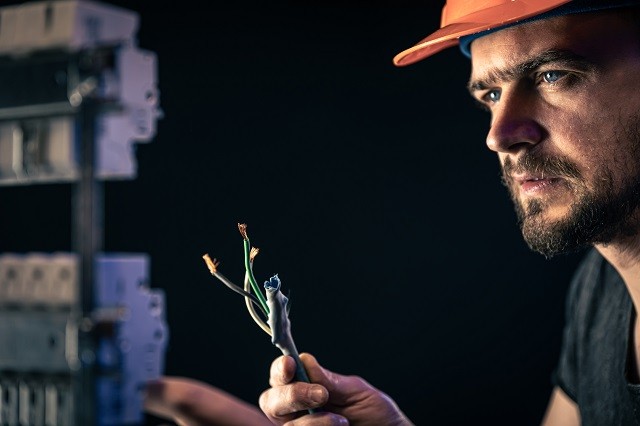
Power cable core breakage refers to the partial or complete rupture or damage to the conductive core within an electrical cable. The core of a power cable typically consists of one or multiple conductors, which carry electrical current from a power source to connected devices or equipment. Core breakage can occur due to various factors, including mechanical stress, environmental conditions, manufacturing defects, or age-related degradation.
Ⅲ. Consequences of Core Breakage
A. Electrical Faults
a. Short circuits occur when the conductors within the cable come into direct contact, bypassing the load and creating a low-resistance path for current flow.
b. Open circuits occur when the cable core is severed or disconnected, interrupting the flow of current and causing equipment malfunction or failure.
c. Ground faults occur when current leaks from the cable core to ground, posing electrical hazards and potential shock hazards to personnel.
B. Safety Hazards
a. Electrical arcing, sparking, or overheating associated with core breakage can ignite flammable materials, leading to fire hazards and property damage.
b. Exposure to live conductors or energized equipment resulting from core breakage poses electrocution hazards and potential risks of injury or fatality to maintenance personnel or bystanders.
C. Environmental Impact
a. Core breakage may have environmental consequences, such as the release of hazardous substances or pollutants associated with electrical fires or equipment failures.
b. Oil-filled cables, commonly used in high-voltage applications, may leak dielectric fluid or insulating oil if the cable core is damaged, posing environmental contamination risks.
Ⅳ. Warning Signs and Symptoms of Power Cable Core Breakage
Visible Damage: Visual inspection is often the first line of defense against power cable core breakage. Look for visible signs of damage such as cracks, cuts, abrasions, or bulges in the cable's insulation, shielding, or armor layers.
Insulation Breakdown: Insulation breakdown is a significant concern in power cable core breakage. Watch for indications such as discoloration, brittleness, or flaking of the insulation material.
Overheating: Excessive heat generation along the length of the cable may signal core breakage or insulation breakdown. Monitor for hotspots or areas of localized heating on the cable's surface, which may indicate increased resistance due to core breakage or conductor degradation.
Odor or Burning Smell: A noticeable odor or burning smell near the cable installation may suggest insulation breakdown or core breakage, accompanied by thermal degradation of the cable's components.
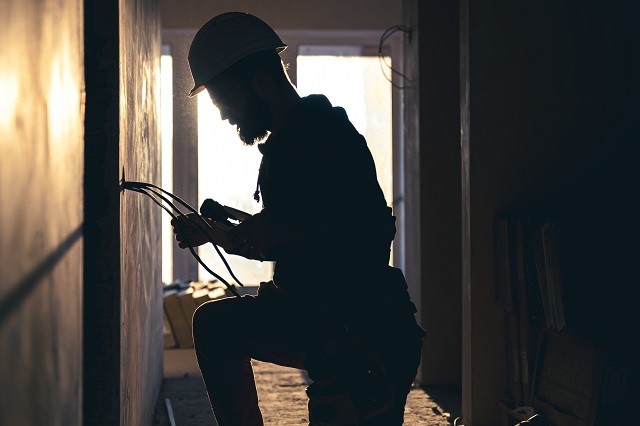
Abnormal Noise: Unusual sounds such as buzzing, crackling, or hissing coming from the cable installation may be indicative of partial discharge or corona activity associated with core breakage or insulation defects.
Electrical Fluctuations: Fluctuations in voltage or current levels, as well as irregularities in power quality parameters, may point to core breakage or electrical faults in power cables. Monitor for voltage dips, surges, or frequency variations that could result from intermittent contact or discontinuity in the cable's core.
Ⅴ. Power cable broken core prevention
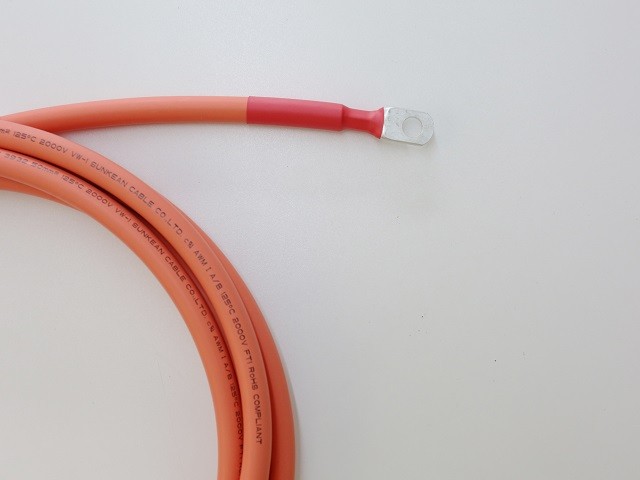
Proper Installation Techniques:
a. Ensure cables are installed by qualified personnel following manufacturer guidelines and industry standards.
b. Avoid sharp bends, kinks, or excessive tension during installation.
c. Use appropriate cable pulling equipment and lubricants to minimize friction and mechanical strain on the cable core.
Careful Cable Routing:
a. Plan cable routes to minimize exposure to mechanical stressors such as sharp edges, corners, or equipment.
b. Maintain proper separation between power cables and other infrastructure, including communication cables, plumbing, and structural elements.
c. Avoid routing cables through areas prone to vibration, excessive movement, or exposure to harsh environmental conditions.
Protective Measures:
a. Use cable trays, conduits, or ducts to shield cables from physical damage and environmental hazards.
b. Install cable supports, clamps, and hangers to secure cables and prevent sagging or excessive movement.
c. Implement cable management systems to organize and protect cables, reducing the risk of accidental damage during maintenance or operations.
Proper Grounding and Bonding:
a. Ensure proper grounding and bonding of cable shields and armor to minimize the risk of induced voltages, electromagnetic interference (EMI), and electrical faults.
b. Use high-quality grounding materials and connections to maintain low impedance paths for fault currents and stray currents.
Ⅵ. Repair and remediation of broken cores in power cables
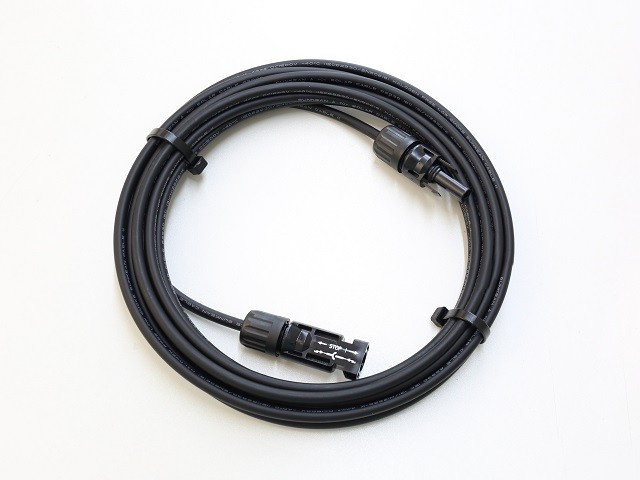
A. Discuss strategies for repairing power cable core breakage
Core Repair or Replacement: Depending on the severity of the damage, the broken core may need to be repaired or replaced. Techniques such as splicing or welding can be used to reconnect severed cores, ensuring continuity of electrical conductors. In cases of extensive damage, a section of the cable may need to be replaced entirely.
Insulation and Shielding Restoration: After the core repair or replacement, the insulation and shielding layers must be restored to their original condition. This may involve applying new insulation materials, such as heat shrink tubing or resin-filled sleeves, and reinstating shielding layers to ensure proper electrical insulation and protection against environmental factors.
B. Follow manufacturer recommendations and industry best practices
Ensuring Compatibility and Integrity: Manufacturers provide specific recommendations for repairing their cables based on their design, materials, and construction. Following these recommendations ensures that repair materials and techniques are compatible with the cable's specifications, preserving its integrity and performance.
Optimizing Long-Term Performance: Manufacturer recommendations and industry best practices are based on extensive research, testing, and field experience. By following these guidelines, repair professionals can leverage the knowledge and expertise accumulated over years of industry practice, optimizing the long-term performance and reliability of repaired cables.
C. Evaluate the effectiveness of the repair and verify the integrity of the repaired cable core
Visual Inspection: Begin by conducting a thorough visual inspection of the repaired cable cores. Look for any signs of damage, such as cuts, abrasions, or irregularities in the insulation or shielding layers. Ensure that the repaired section matches the surrounding cable in terms of appearance and consistency.
Insulation Resistance Testing: Perform insulation resistance (IR) testing to assess the insulation integrity of the repaired cores. Use a megohmmeter to measure the resistance between the repaired core and the cable's metallic shield or armor. A high resistance reading indicates effective insulation, while a low reading may indicate insulation damage or moisture ingress.
Hi-Pot Testing: Conduct high-potential (Hi-Pot) testing to verify the dielectric strength of the repaired cable cores. Apply a high voltage between the repaired core and the metallic shield or armor while monitoring for any signs of breakdown or flashover. A successful Hi-Pot test confirms the integrity of the insulation and the effectiveness of the repair.
Continuity Checks: Verify the continuity of the repaired cable cores using a continuity tester or multimeter. Ensure that there are no open circuits or discontinuities in the repaired section of the cable. Test continuity between the repaired core and adjacent conductors or termination points to confirm electrical connectivity.
Ⅶ. Conclusion
If you are interested in high-quality cables and comprehensive after-sales service, welcome to visit SUNKEAN, where there are all kinds of latest cable products you need. If you have any needs, you can leave a message to our salesman, thank you for your coordination. Email: wendy@sunkean.com