Why Photovoltaic Cables Need Irradiation Cross-Linking: Enhancing Durability and Safety in Solar Power Systems
- Share
- Issue Time
- Apr 15,2025
Summary
Why do photovoltaic cables need irradiation cross-linking?
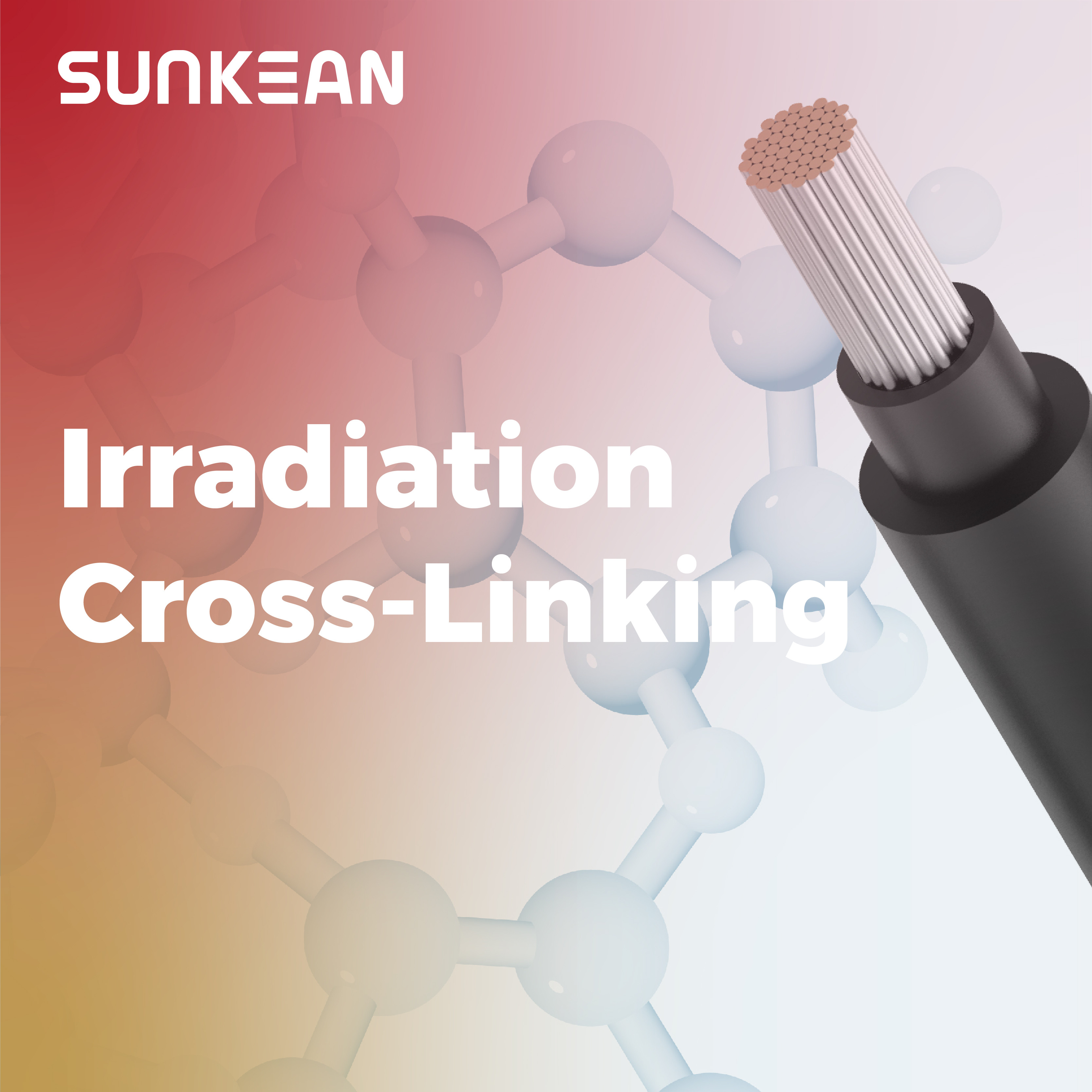
Why Photovoltaic Cables Need Irradiation Cross-Linking?
As the world accelerates its shift toward clean and renewable energy, solar power has emerged as a frontrunner in the transition to sustainability. At the heart of any photovoltaic (PV) power system are its electrical components, and none are more vital than the solar cables. These cables serve as the connective tissue of the solar installation, transmitting power from photovoltaic modules to inverters, combiner boxes, and finally into the grid. Given their indispensable role and constant exposure to the elements, solar cables face unique challenges that ordinary cables do not.
This is why specialized PV cables are engineered with enhanced physical and chemical properties. One groundbreaking technology that has significantly improved the performance and longevity of PV cables is irradiation cross-linking. This technique transforms conventional insulation materials into robust, long-lasting compounds capable of withstanding the extreme conditions that solar power systems encounter. In this in-depth article, we explore why irradiation cross-linking is essential for PV cables, how the process works, and the substantial benefits it offers.
The Unique Demands of Solar Cable Applications
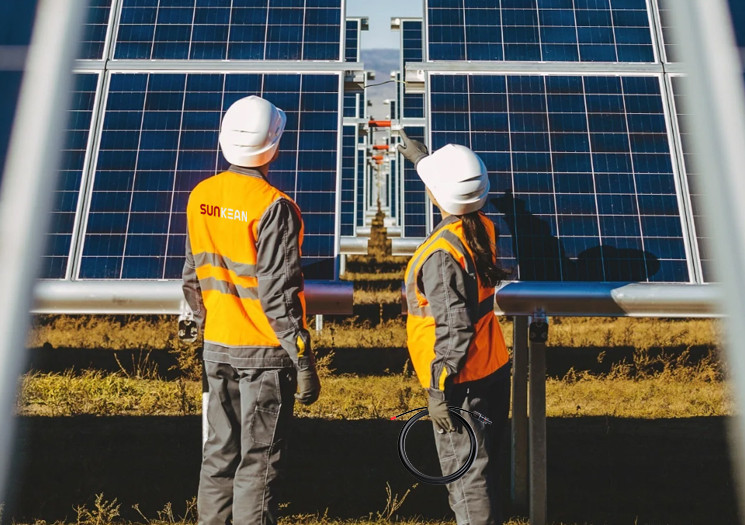
Photovoltaic systems operate in some of the harshest environments on Earth—deserts, rooftops, remote plains, or floating solar farms. The cables used in these systems must function reliably for 25 years or more under continuous exposure to the sun and extreme environmental conditions. These include:
· Ultraviolet (UV) Radiation: Constant sun exposure degrades the outer sheath of standard cables, causing brittleness and cracking over time.
· Thermal Fluctuations: Temperatures can swing dramatically from below freezing at night to over 100°C in the afternoon sun.
· Humidity and Moisture: In coastal or tropical regions, high humidity accelerates corrosion and insulation breakdown.
· Mechanical Stress: Bending during installation, vibration, and wind load can damage weaker cables.
These challenges make it clear that solar cables must be designed for maximum durability and reliability. The insulation and sheath materials must exhibit high resistance to heat, wear, and environmental degradation—qualities that irradiation cross-linking helps deliver.
What Is Irradiation Cross-Linking?
Irradiation cross-linking, also referred to as electron beam (EB) cross-linking, is a high-tech method of altering the molecular structure of polymers—commonly used in cable insulation and sheathing—to enhance their physical properties. When high-energy electron beams penetrate materials such as polyolefins, they are like countless molecular scalpels working simultaneously, cutting off all the weak links in the original molecular chains and then re-welding them into a dense three-dimensional network structure. This is what is called "cross-linking."
Unlike traditional chemical cross-linking, which requires additives and high temperatures, irradiation cross-linking uses no chemical cross-linkers and is performed at relatively low temperatures, making it a greener, cleaner process. The result is a cross-linked polymer that is thermoset in nature—it retains its shape and strength under heat and stress.
The Science Behind Cross-Linking
The irradiation cross-linking process can be broken down into several key phases:
· Ordered Cross-Linking Period: During this phase, terminal groups of polymer chains link up, initiating a basic molecular network.
· Amorphous Cross-Linking: Non-crystalline regions of the polymer begin to cross-link extensively, improving elasticity and toughness.
· Crystalline Breakthrough: Molecules at the edge of crystalline regions also start to cross-link, enhancing overall structural integrity.
· Complete Reconstruction: The polymer transitions to a fully cross-linked state, forming a dense, uniform three-dimensional network. This network structure significantly enhances the thermal, mechanical, and chemical resistance properties of the material.
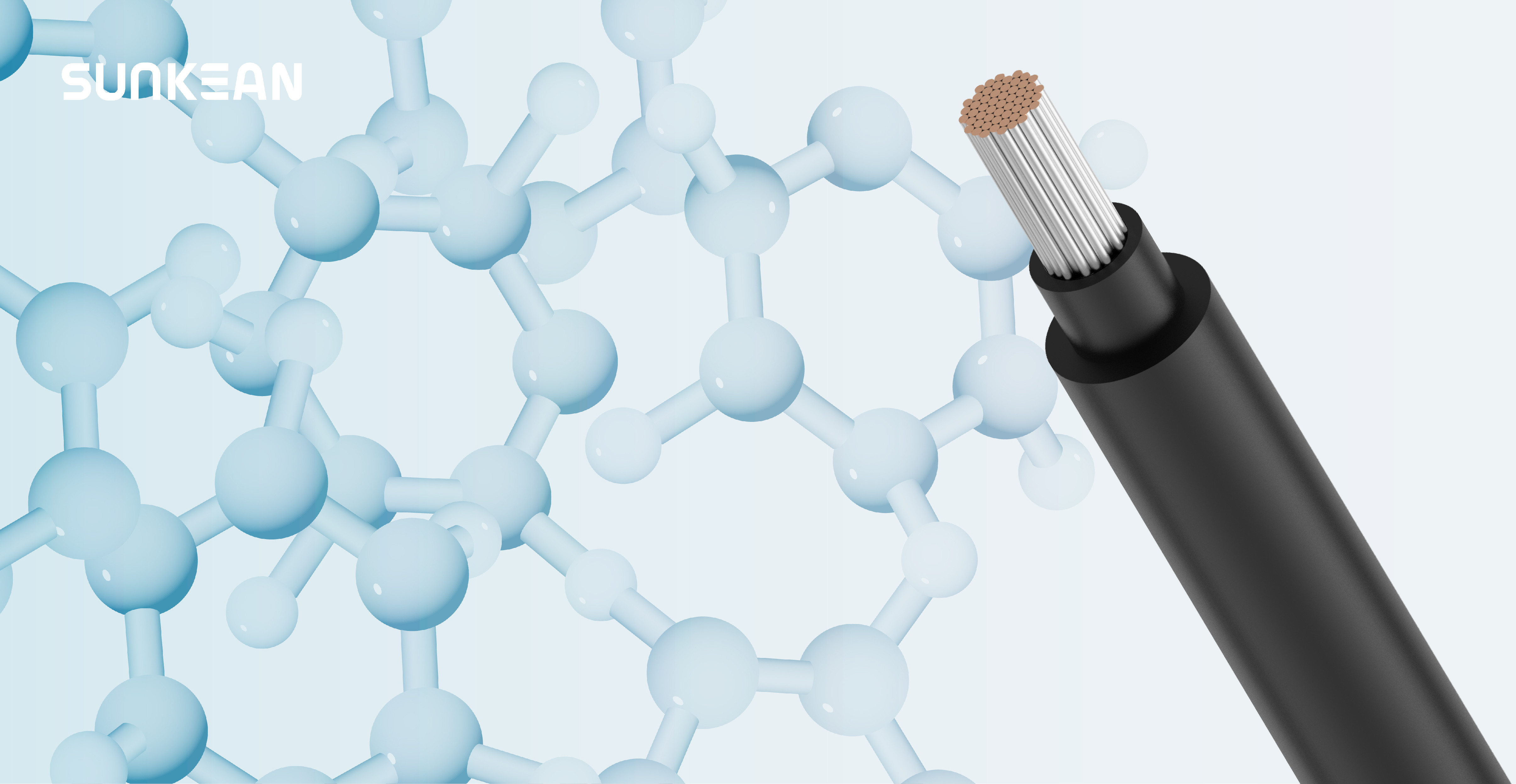
How the Irradiation Process Works
To carry out this transformation, an electron accelerator is used. The process involves several key steps:
· Standard 380V industrial three-phase power is converted to a 400Hz medium-frequency supply via a frequency conversion system.
· This power drives a steel cylinder within the accelerator, where high-voltage electricity (up to 20kV) is generated.
· Through a series of components like magnetic conductors and transformers, the energy is converted into a stream of high-energy electrons.
· These electrons are directed toward the polymer, penetrating its molecular structure and triggering cross-linking.
The entire process is tightly controlled and leaves no chemical residue, making it ideal for green manufacturing and high-performance product design.
Key Advantages of Irradiation Cross-Linked PV Cables
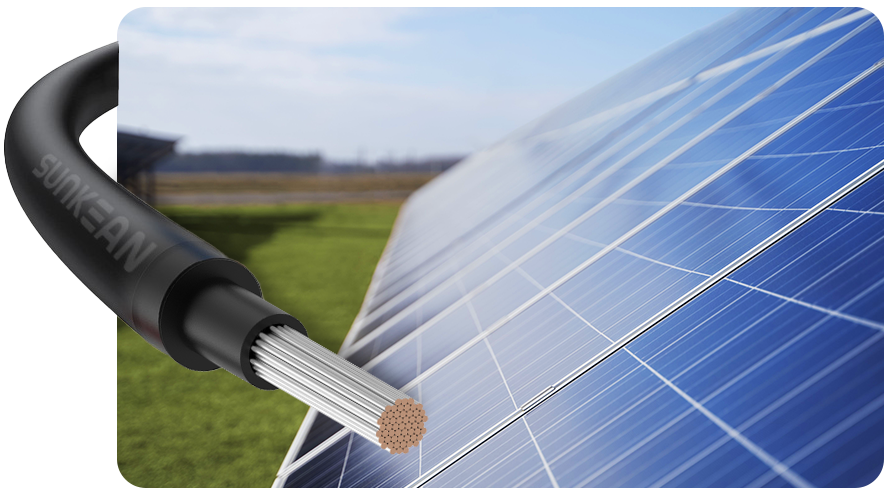
1. Superior Heat Resistance
Cross-linked PV cables can withstand temperatures up to 150°C—significantly higher than the 90°C limit of non-cross-linked cables. This makes them ideal for solar farms in high-temperature regions such as the Middle East, Africa, or southwestern United States. Even under direct sunlight, the cable insulation maintains its integrity and performance, avoiding softening, sagging, or melting.
2. Long-Term Thermal Stability
The dense molecular network formed by cross-linking reduces the mobility of polymer chains, slowing down oxidation and aging. This translates into a significantly extended thermal aging life, maintaining insulation resistance and electrical performance for decades.
3. Enhanced Mechanical Strength
Cross-linked PV cables exhibit 3-5 times the tensile strength of standard cables. This means they are better able to resist: Crushing and impact, Abrasion during installation, Vibration from wind or movement, and Damage from rodents and pests.
4. Superior Flame Retardance and Safety
Cross-linked solar cables often use halogen-free compounds. In case of fire, these cables do not emit toxic gases and form a charred carbon layer that resists flame propagation. This makes them suitable for applications where safety is paramount, such as schools, hospitals, and residential rooftops.
5. UV and Weather Resistance
The cross-linked sheath resists photochemical degradation caused by UV rays, ozone, and other environmental factors. This high level of resistance is particularly important in solar installations that face prolonged sun exposure and rapidly changing weather conditions. For example, in desert regions or high-altitude solar farms, intense UV radiation can quickly break down standard polymer insulation. Cross-linked PV cables maintain their structural integrity and insulation performance, preventing issues like cracking, chalking, discoloration, or the loss of dielectric strength. Furthermore, they remain flexible and resistant to embrittlement, which allows them to perform reliably across a wide range of climates—from arid deserts to rainy tropics.
This UV and weather resistance ensures that cross-linked PV cables maintain peak performance over the lifespan of the installation, which is often 25 years or more. This reduces the need for costly replacements or maintenance and ensures the uninterrupted operation of solar power systems.
6. Chemical Resistance
Cross-linked materials are less permeable to moisture and resistant to many chemicals, including oils, solvents, acids, and alkaline substances. In solar farms located in agricultural areas, the cables may come into contact with fertilizers, pesticides, and irrigation water—all of which can be corrosive to conventional cable materials. In coastal areas, salt-laden air and humidity present an equally corrosive environment that can cause insulation failure if the cable isn't properly protected.
Irradiated PV cables provide a high level of protection against these chemical exposures, ensuring safe and stable power transmission even under aggressive environmental conditions. Additionally, in industrial solar installations where oils, fuels, and airborne chemicals may be present, cross-linked cables remain robust and reliable. Their chemical resilience extends the operational life of solar infrastructure and minimizes system downtime caused by insulation degradation or short circuits.
Practical Applications: Where Irradiated PV Cables Excel
Given their enhanced properties, irradiation cross-linked PV cables are ideal for a wide range of solar power applications:
· Utility-Scale Solar Farms: Where exposure to heat and UV radiation is intense and cables need to last for 25+ years without failure.
· Rooftop Solar Systems: Cables are often laid directly on rooftops, exposed to the elements and temperature fluctuations.
· Floating PV (FPV) Installations: Where humidity, corrosion, and constant movement make cross-linking essential.
· BIPV (Building-Integrated Photovoltaics): Where fire safety and long-term aesthetics are important.
· Agrivoltaic Installations: Where exposure to pesticides, irrigation, and mechanical contact with equipment is common.
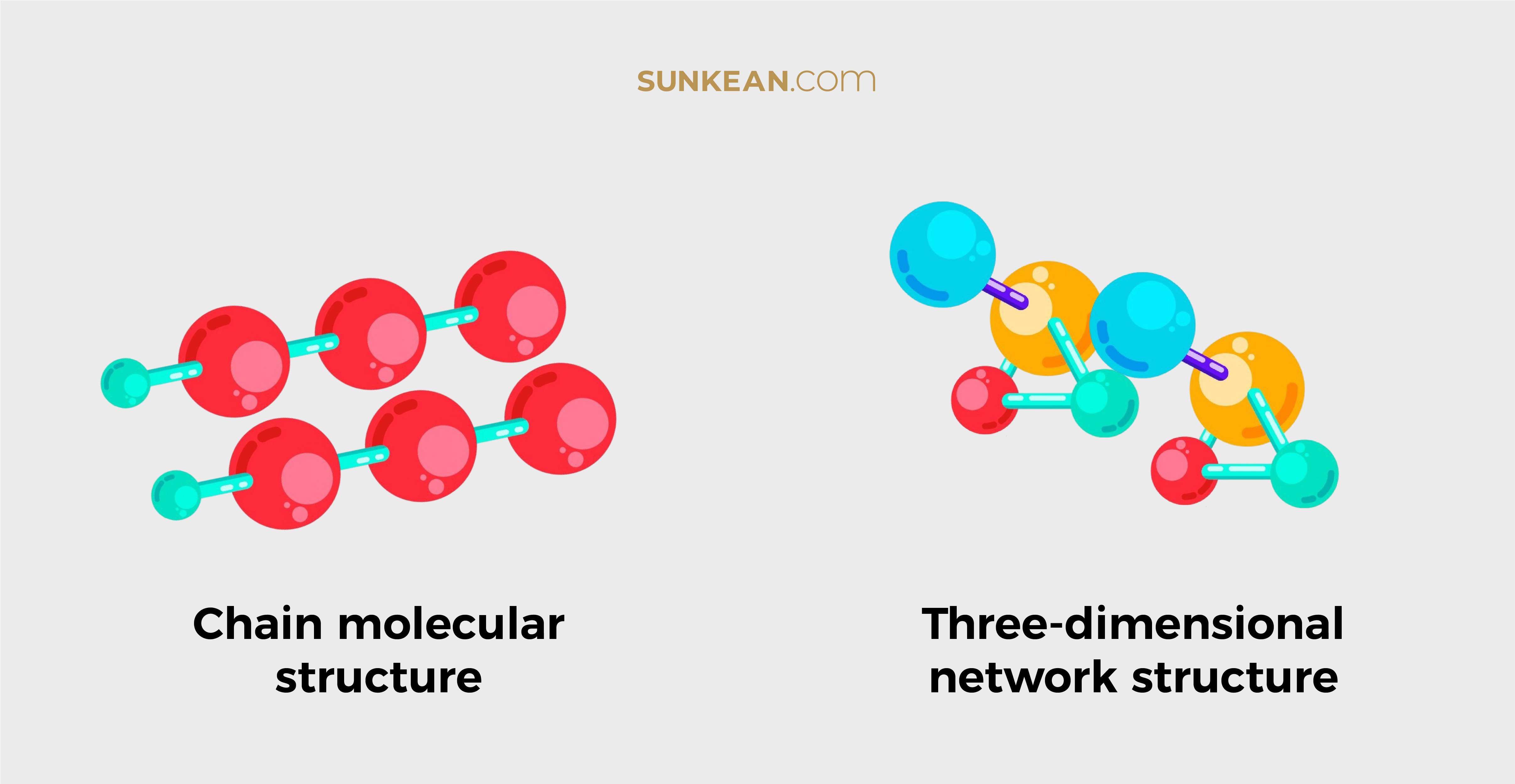
Environmental and Sustainability Benefits:
As the world shifts toward low-carbon, renewable energy solutions, it is no longer enough for solar power systems to merely generate clean electricity. The materials and technologies used within those systems must also embody the principles of sustainability, safety, and environmental responsibility. In this context, irradiation cross-linking technology used in solar cables and PV cables represents a major leap forward.
Traditional cross-linking methods for cable insulation typically rely on chemical agents, such as peroxides or silane compounds, which initiate polymer bonding through heat and pressure. While effective, these chemical agents can:
· Release volatile organic compounds (VOCs) during processing
· Leave behind residual chemicals that may degrade over time
· Require additional manufacturing steps for curing, which increases energy use and operational complexity
In contrast, irradiation cross-linking is a non-chemical, low-emission alternative. It uses electron beam technology to directly modify the molecular structure of insulation materials without introducing any additives. This results in:
· No chemical residue in the final product
· No curing ovens, which saves energy and reduces carbon emissions
· No off-gassing, creating a safer and cleaner working environment in the manufacturing process
This not only aligns with the principles of green manufacturing but also supports stricter environmental compliance and ESG (Environmental, Social, and Governance) standards increasingly demanded by global markets and regulators.
Conductor: 1×1.5~400mm²
Insulation Color: Optional color
Jacket Color: Optional color
Conductor: 2.5~6mm²
Color: Black, red or other colors
Conductor: 1×10~400mm²
Insulation Color: Black
Jacket Color: Black
Conductor: 18AWG~2000kcmil
Color: Black, red or other colors
Another important sustainability benefit of irradiation cross-linked PV cables is their significantly extended service life. These cables are engineered to withstand extreme temperatures, UV radiation, mechanical abrasion, and chemical exposure over decades. As a result:
· Fewer cables need to be replaced over the 25–30 year lifespan of a photovoltaic installation
· Maintenance costs and system downtimes are minimized
· Material waste is dramatically reduced, especially in large-scale utility projects
As solar energy continues to expand globally, especially in regions with harsh environmental conditions, the demand for durable, high-performance cables will grow. Irradiated PV cables represent a vital innovation that ensures systems remain reliable and safe over their full life span.
Whether you're an EPC contractor, system designer, or solar project investor, specifying irradiation cross-linked solar cables is a smart decision that pays off in reduced maintenance, enhanced safety, and long-term performance.