Analysis of the Trend of Aluminum Solar Cables Replacing Copper Solar Cables
- Share
- Issue Time
- Apr 23,2025
Summary
This article explains in detail why the solar cable market is beginning to prefer aluminum cables to copper cables, as well as the advantages of aluminum cables and the difficulties in the R&D and implementation process.
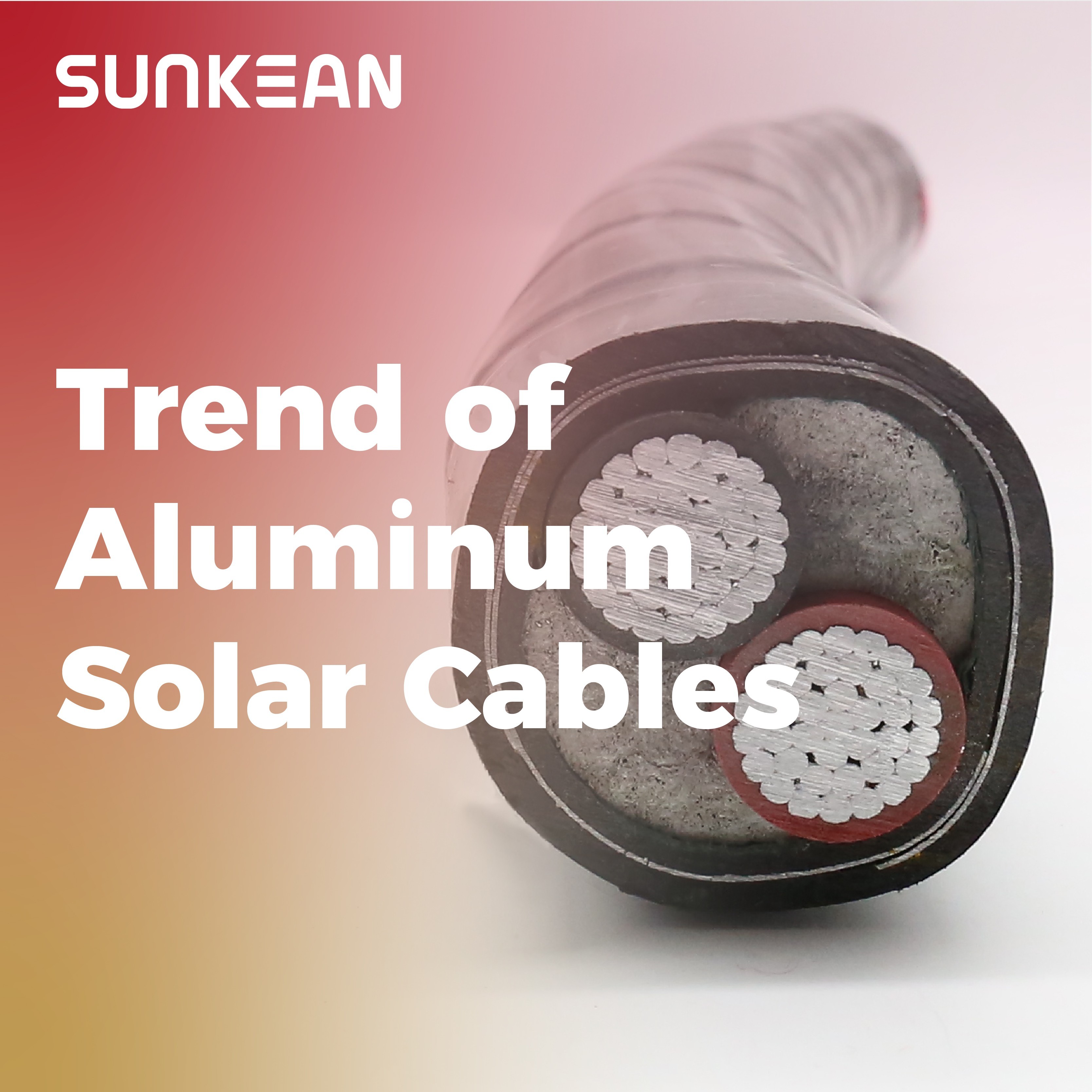
With the growth of global photovoltaic installed capacity (according to IEA data, tripling global renewable power capacity by 2030 is an ambitious but achievable goal), power station construction has shifted from "extensive expansion" to "fine cost reduction", while expanding the area of photovoltaic projects, people began to pursue a balance between cost and quality. Although traditional copper core cables have excellent conductivity, the high cost of raw materials and weight disadvantages seriously restrict the cable deployment efficiency of large ground power stations and the return on investment of distributed projects. In this context, aluminum conductor solar cables have become the key solution to solve the contradiction between cost and performance with material innovation and process upgrades. Aluminum conductor solar cables are becoming the preferred solution for distributed and large power stations with the following core advantages:
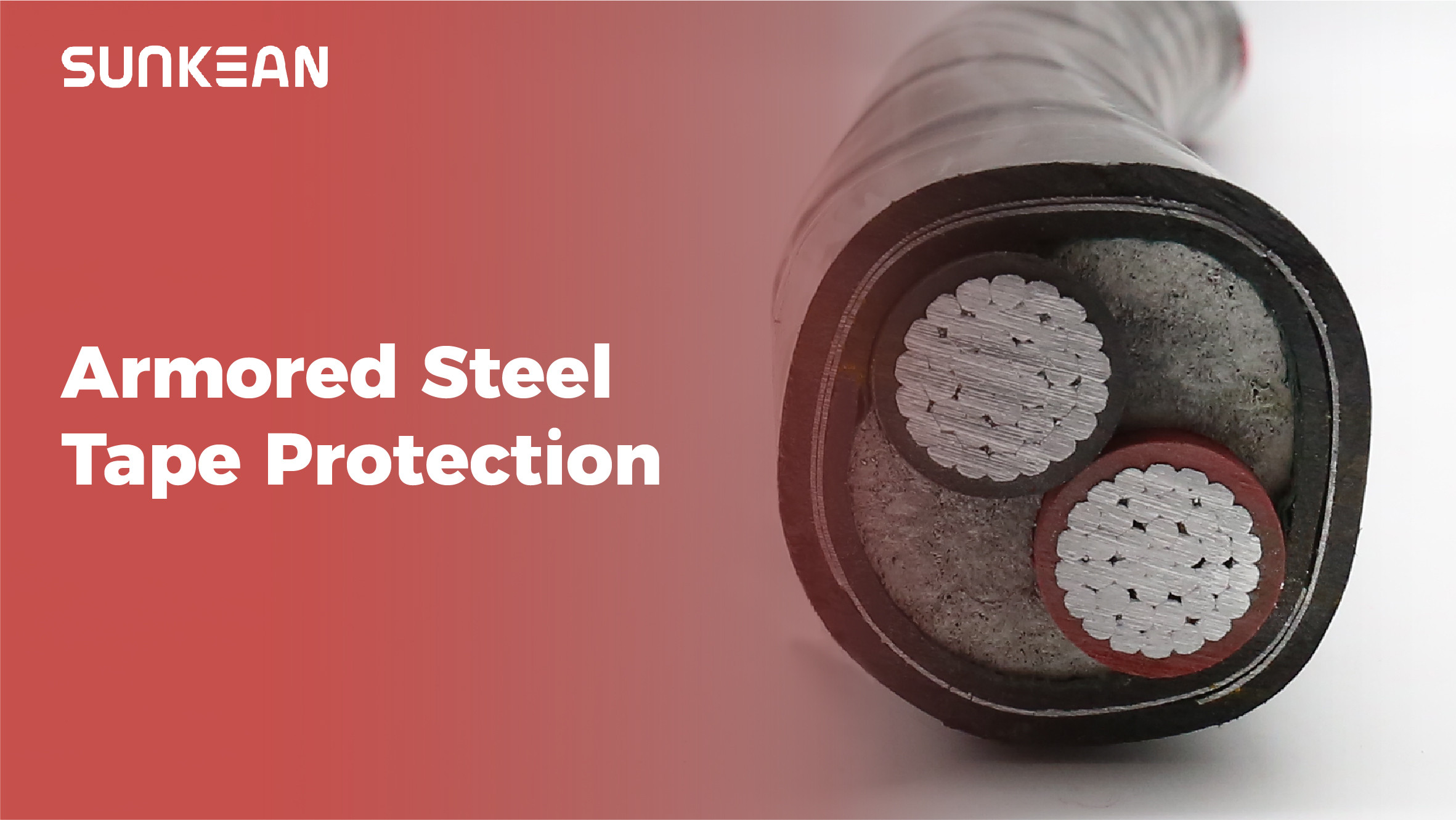
Under the same conductivity, the price per kilogram of aluminum is about 30-50% cheaper than copper, and this price gap will become more obvious as the scale of photovoltaic projects expands.
EPC can achieve considerable project cost reduction by replacing copper photovoltaic wires with aluminum photovoltaic wires, optimizing the budget without affecting the power operation effect.
At the same time, aluminum resources are abundant and the price is stable, which can effectively reduce the purchasing pressure caused by copper price fluctuations.
*In early May, SUNKEAN's CU-AL wiring harness solution will be exhibited at the Munich Energy Exhibition in Germany. You are welcome to visit booth A4.117 for detailed information.
Weight reduction of aluminum conductor solar cables
When the current carrying capacity of the two is the same, the weight of aluminum can be reduced by about 50%~70% compared with copper. After the weight is reduced, solar cables are easier to transport, store and install, which further reduces labor costs and installation time. In addition, for example, in rooftop photovoltaic systems, aluminum wire connection solutions can reduce the weight of the entire roof structure by virtue of their weight advantage, which is crucial for projects with building load safety restrictions.
Conductor: 1×10~400mm²
Insulation Color: Black
Jacket Color: Black
Conductor: 2×10~400mm²
Insulation Color: Black & red
Jacket Color: Red
An exceptional tool designed for seamlessly connecting string harnesses to combiner boxes or string inverters.
Conductor: 1×2.5~400mm²
Insulation Color: Black
Jacket Color: Black
Aluminum conductor solar cables are environmentally sustainable
Aluminum is the most abundant metal element in the earth's crust (accounting for about 8%), while copper reserves are only 1/20 of aluminum, and global copper resources are facing the risk of depletion (copper mines are expected to only be mined for 30-40 years). From a sustainable perspective, carbon footprint indicators can be used as another metric. Carbon footprint accounting covers the entire cycle of raw material mining, production, transportation and recycling. In the production process of aluminum conductors, carbon emissions are more than 70% lower than those of copper conductors. For a 100MW photovoltaic power station, the carbon emissions of aluminum solar cables in the entire life cycle are about 35% lower than those of copper solar cables, which meets the strict requirements of the EU, France and other countries and regions for the carbon footprint of photovoltaic products. With the technological innovation of cables, such as the steel-belt armored aluminum solar cable developed by SUNKEAN, which takes into account corrosion resistance and production energy consumption optimization, it can effectively reduce the risk of heavy metal pollution and protect the quality of the earth's environment.
Technical Difficulties and Safety Hazards of Cable Copper-Aluminum Conversion
In photovoltaic systems, the direct connection of copper-aluminum conductors forms multiple technical bottlenecks due to differences in material properties. SUNKEAN has invested a lot of R&D efforts to launch a low-loss, highly stable copper-aluminum transfer method, and is committed to providing customers with a one-stop copper-aluminum cable connection solution.
Electrochemical corrosion phenomenon of aluminum cables
The electrode potential difference between copper and aluminum will form a galvanic effect, which will accelerate the oxidation of aluminum in a humid environment, resulting in increased contact resistance, local heating and even fire.
How does this phenomenon occur? When copper and aluminum are in direct contact, the two metals form a micro-battery in the electrolyte (such as rainwater, humid air), with aluminum rapidly oxidizing and dissolving as the anode and copper remaining stable as the cathode. This process will generate insulating substances such as aluminum oxide (Al₂O₃), causing the contact resistance to surge from the initial micro-ohm level to the kilo-ohm level, and the local temperature can exceed 200°C.
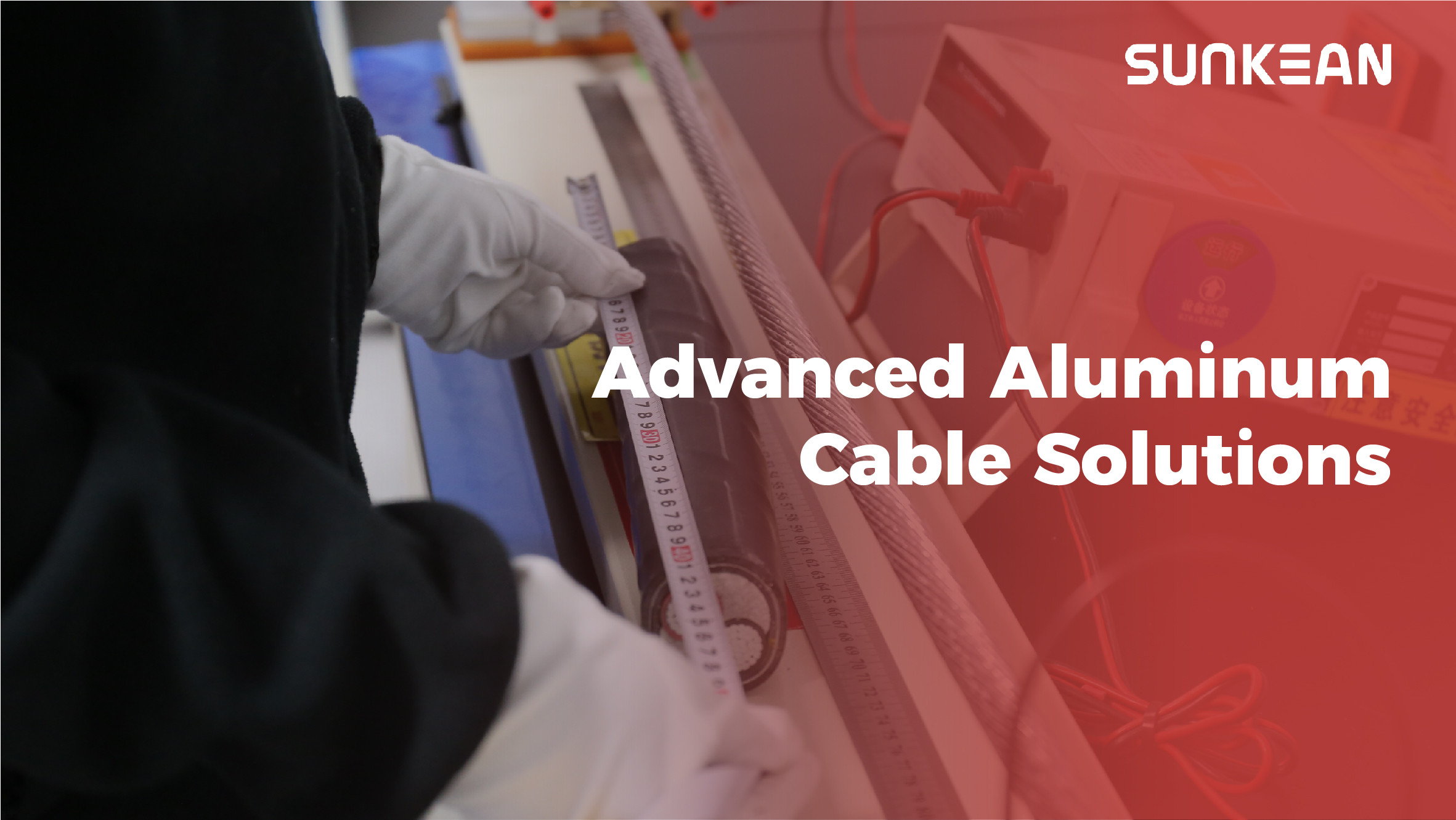
In addition, studies have shown that copper-aluminum joints can develop a significant corrosion layer in a salt spray environment in just 30 days, with a contact resistance increase of more than 300%. Therefore, international standards clearly require that transition technology must be used for copper-aluminum connections, such as copper-aluminum transition terminals and plating treatments.
Differences in thermal expansion and mechanical properties of aluminum cables
The thermal expansion coefficient of aluminum is larger than that of copper. In photovoltaic power stations with large temperature differences between day and night, the joints will produce micron-level displacements due to repeated thermal expansion and contraction, resulting in loosening of the crimping points. Experiments show that after 1,000 hot and cold cycles, the contact resistance of aluminum joints increases by an average of 35%, while that of copper only increases by 8%. In addition, aluminum has low creep strength (about 50MPa) and is prone to plastic deformation under long-term current load, further exacerbating the risk of connection failure. SUNKEAN has taken targeted solutions to the thermal expansion and creep response of aluminum, and finally achieved a perfect balance between the electrical parameters and application stability of aluminum conductor cables.
Limitations of traditional connection processes for aluminum cables
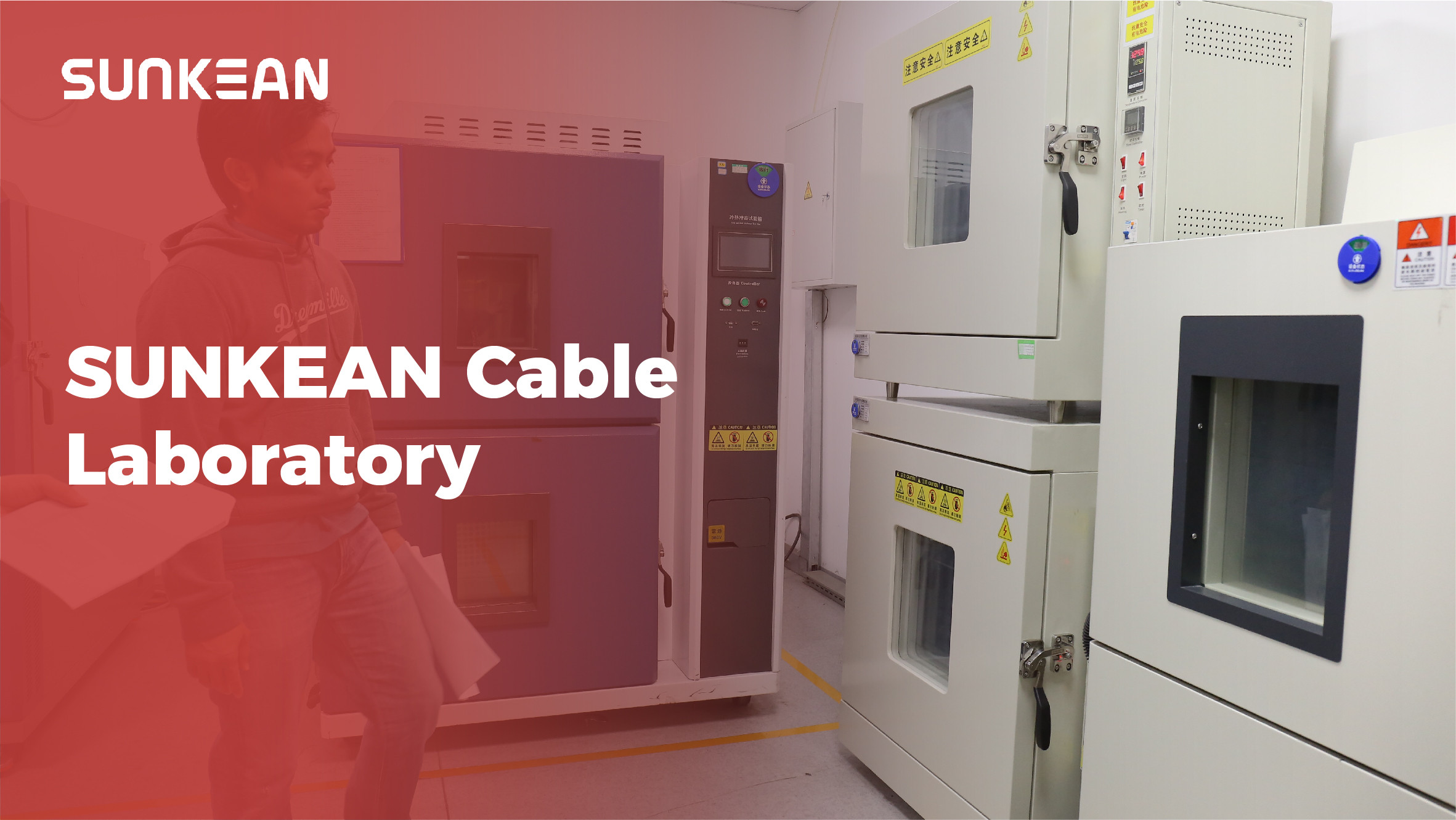
The resistivity of the natural oxide layer (Al₂O₃) on the surface of aluminum is extremely high, and it is difficult to completely destroy this layer with traditional crimping processes, resulting in a reduction of more than 60% in the effective conductive area. For example, after crimping a 6mm diameter aluminum wire, the actual conductive cross-section may be less than 40% of the nominal value. In addition, due to size limitations, small-section cables are difficult to match standard copper-aluminum transition terminals, forcing the construction party to adopt temporary measures such as copper wire winding, further increasing safety hazards.
In addition to the original welding techniques, SUNKEAN will also conduct tensile tests, profile analysis, and temperature rise tests on finished products to solve the crimping problems of aluminum solar cables, ensuring that the aluminum solar cables can maintain a service life of up to 25 years in terms of both internal structure and external performance.
In addition to strict control of the production process, SUNKEAN also develops supporting crimping tools and full-specification terminal products, and provides professional crimping step guidance and copper-aluminum cable specification comparison selection table, using rich project implementation experience to solve various problems that customers may encounter during the installation process.
Future Trends: How does aluminum conductor technology promote changes in the photovoltaic industry?
The three major difficulties in copper-aluminum conversion are closely linked, and breakthroughs need to be achieved through the collaborative innovation of materials science, process engineering, and standardized design. With the popularization of international standards, the reliability and economy of aluminum conductor solar cables will be further improved, becoming the mainstream choice for green energy transmission. With the breakthrough of high-conductivity aluminum alloy materials, the substitution capacity of aluminum conductors in the field of medium-voltage cables has been significantly enhanced. In terms of environmental protection, aluminum's low energy consumption and high recycling rate are in line with the global carbon neutrality goal. Under the trend of intelligence, copper-aluminum terminals with integrated sensors can monitor temperature rise and resistance in real time, prevent failures and improve system safety. It is expected that by 2030, the global aluminum conductor solar cable market will have a significant annual compound growth rate.