Why Tensile Testing Is Critical for Solar Cables: Ensuring the Strength and Reliability of PV Systems
- Share
- Issue Time
- Jul 17,2025
Summary
Discover why tensile testing is essential for solar cables. Learn how solar cable materials, construction, and international standards like IEC 62930 and EN 50618 ensure durability, safety, and long-term performance in solar power systems.
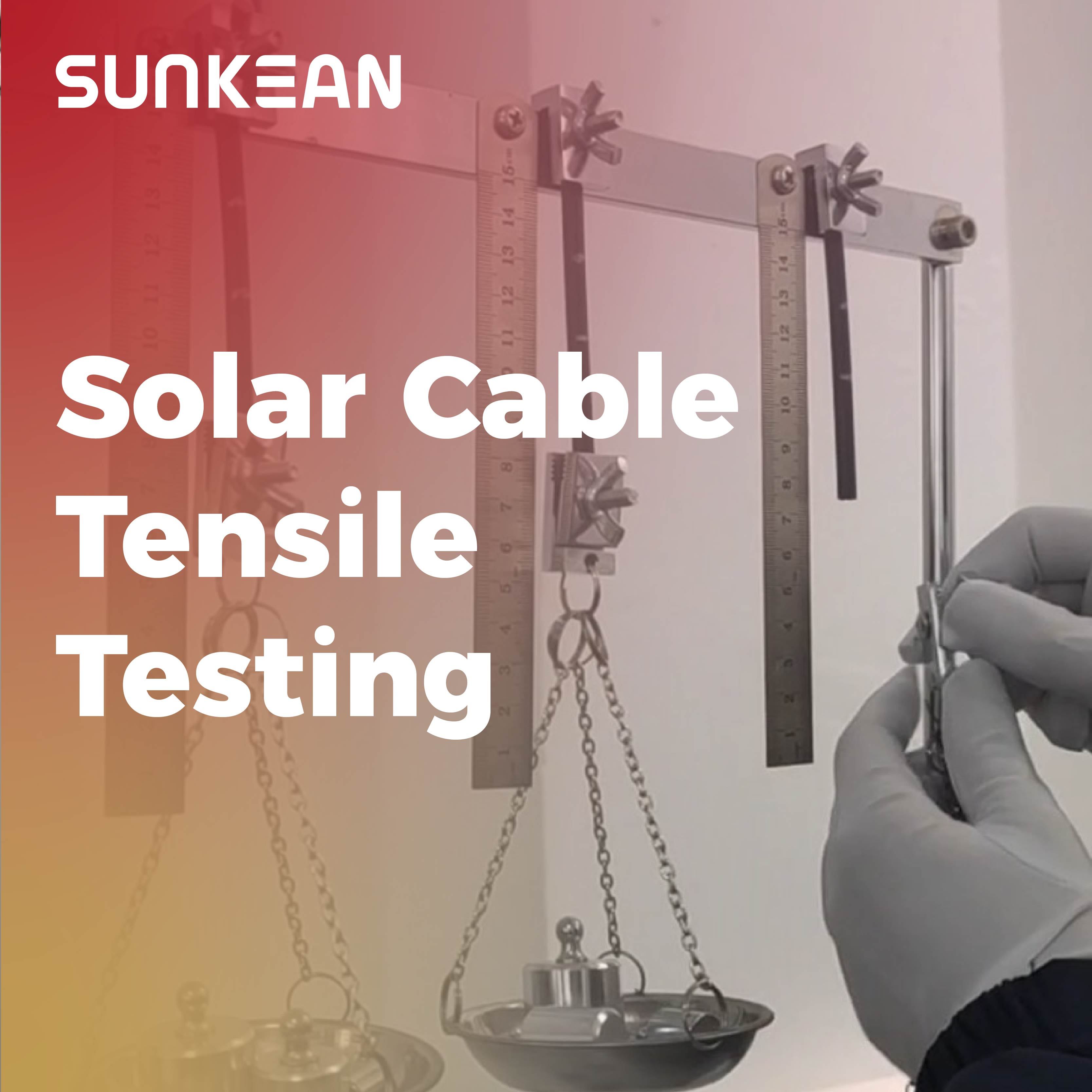
The Role of Solar Cable Tensile Testing in Solar Systems
Solar cables are the critical power pathways connecting key components like PV modules, inverters, and junction boxes within solar power systems. Within the quality assurance framework for solar cables, mechanical testing is an indispensable step, and tensile testing is a crucial part of this.
During installation and maintenance, solar cables are often exposed to extreme temperatures, UV radiation, and various physical stresses. If their mechanical strength, especially tensile strength, is insufficient, cables can easily deform, crack, or even break under pulling forces. Tensile testing is precisely the key method for verifying a cable's ability to withstand such stresses. It ensures the cable's conductor and insulation can endure tension, bending, and long-term mechanical strain without failing. By identifying potential weak points before installation, tensile testing effectively safeguards the long-term safety and stable operation of solar systems. Therefore, tensile strength is a fundamental element determining both cable durability and the overall reliability of the system.
Conductor: 2.5~6mm²
Color: Black, red or other colors
Conductor: 1×1.5~400mm²
Insulation Color: Optional color
Jacket Color: Optional color
Conductor: 12AWG~2000kcmil
Color: Black, red or other colors
Conductor: 1×1.5~400mm²
Insulation Color: Optional color
Jacket Color: Optional color
Definition and Methodology of Solar Cable Tensile Testing
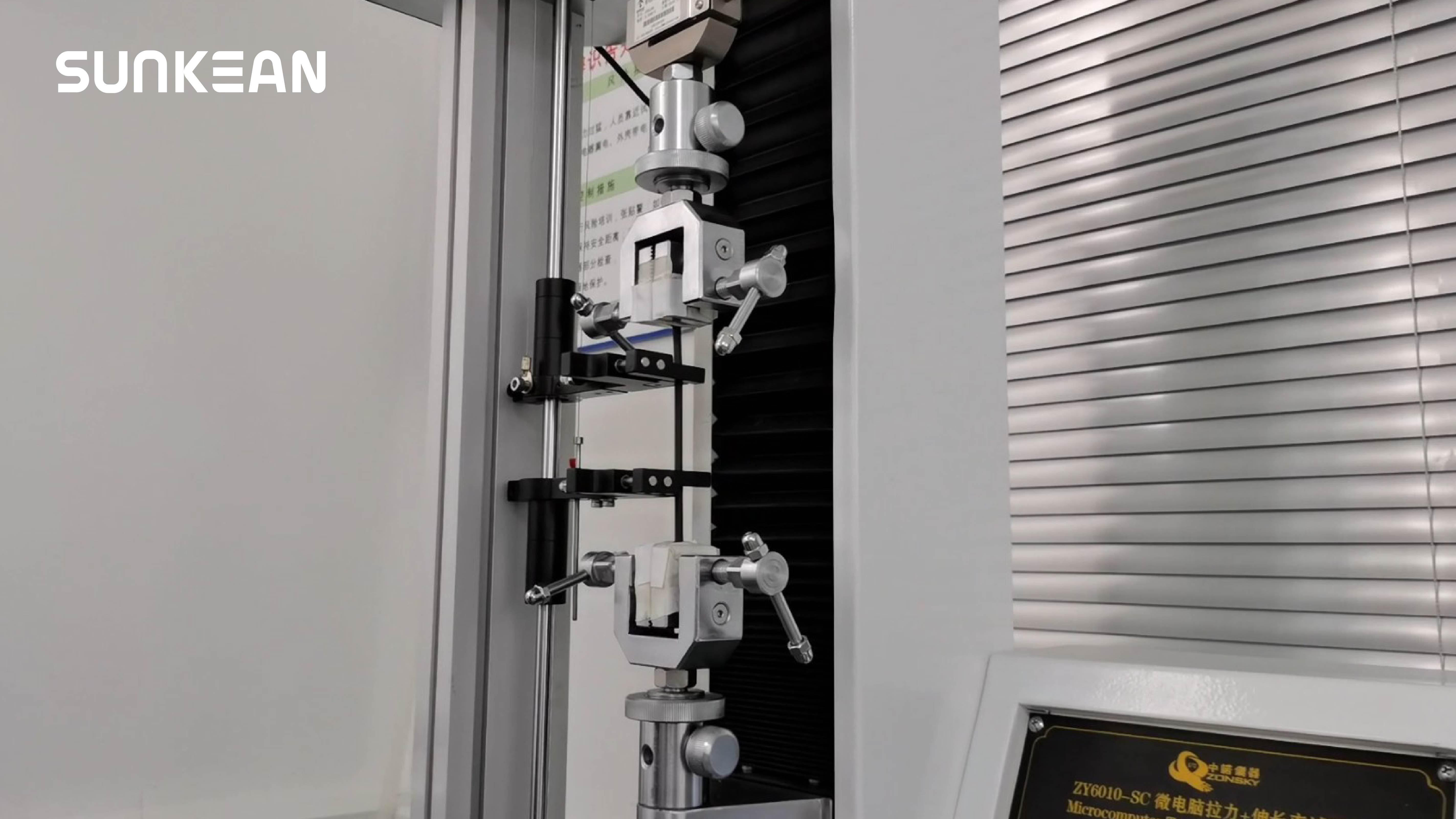
Solar cable tensile testing is a mechanical performance evaluation method designed to measure a cable's ability to resist pulling or tension forces. It quantifies the force a cable can withstand before it begins to permanently deform or ultimately breaks, and is crucial for determining key parameters like the tensile strength and elongation at break of both the conductor and insulation materials. In actual testing, a section of cable sample is clamped at both ends in the grips of a specialized tensile testing machine. The machine pulls the sample at a controlled, constant speed while recording key data, including:
Maximum Tensile Force (Tensile Strength): The highest pulling force the sample withstands before breaking.
Elongation at Break: The percentage increase in the sample's length at the point of breakage compared to its original length.
Yield Strength: The stress point at which the material begins irrecoverable plastic deformation.
These results directly reflect the cable's ability to resist mechanical stress during installation, operation, or maintenance. Tensile testing is a standard procedure in cable manufacturing, used to ensure solar cables meet the mechanical performance requirements specified in international standards like IEC 62930, EN 50618, or UL 4703. By verifying the cable's ability to maintain integrity under pressure, tensile testing provides a solid guarantee for the reliability, safety, and long-term performance of solar power systems.
Why is Tensile Testing Mandatory for Solar Cables?
Tensile testing is central to solar cable quality assurance because it directly verifies whether the cable can withstand the mechanical stresses it will inevitably encounter throughout its entire lifecycle. Unlike cables used indoors, solar cables are deployed outdoors in exposed and often harsh environments – from power plants in arid deserts to rooftops in snowy, windy regions. These environments present unique mechanical challenges, making tensile strength a critical performance indicator.
During daily operation, solar systems continuously endure mechanical and thermal stresses. Ground-mounted systems may experience soil settlement, while rooftop systems can be stressed by wind vibration or structural movement. These factors cause fatigue in the cable material; if its strength and flexibility are inadequate, long-term performance cannot be guaranteed.
During installation, solar cables often need to be pulled through conduits, laid over long distances, or routed around frame corners. Insufficient tensile strength can lead to the cable being stretched, deformed, or even broken, causing damage to the conductor or insulation. Such damage might not show immediately, but accumulated over time, it can lead to power loss, electrical faults, or even fire hazards.
Tensile testing is also key to ensuring product consistency. It guarantees that every batch of cable meets the requirements of international standards like IEC 62930, EN 50618, or UL 4703. By proving the cable possesses both electrical safety and mechanical robustness, tensile testing gives installers, system owners, and end-users confidence in long-term, reliable operation.
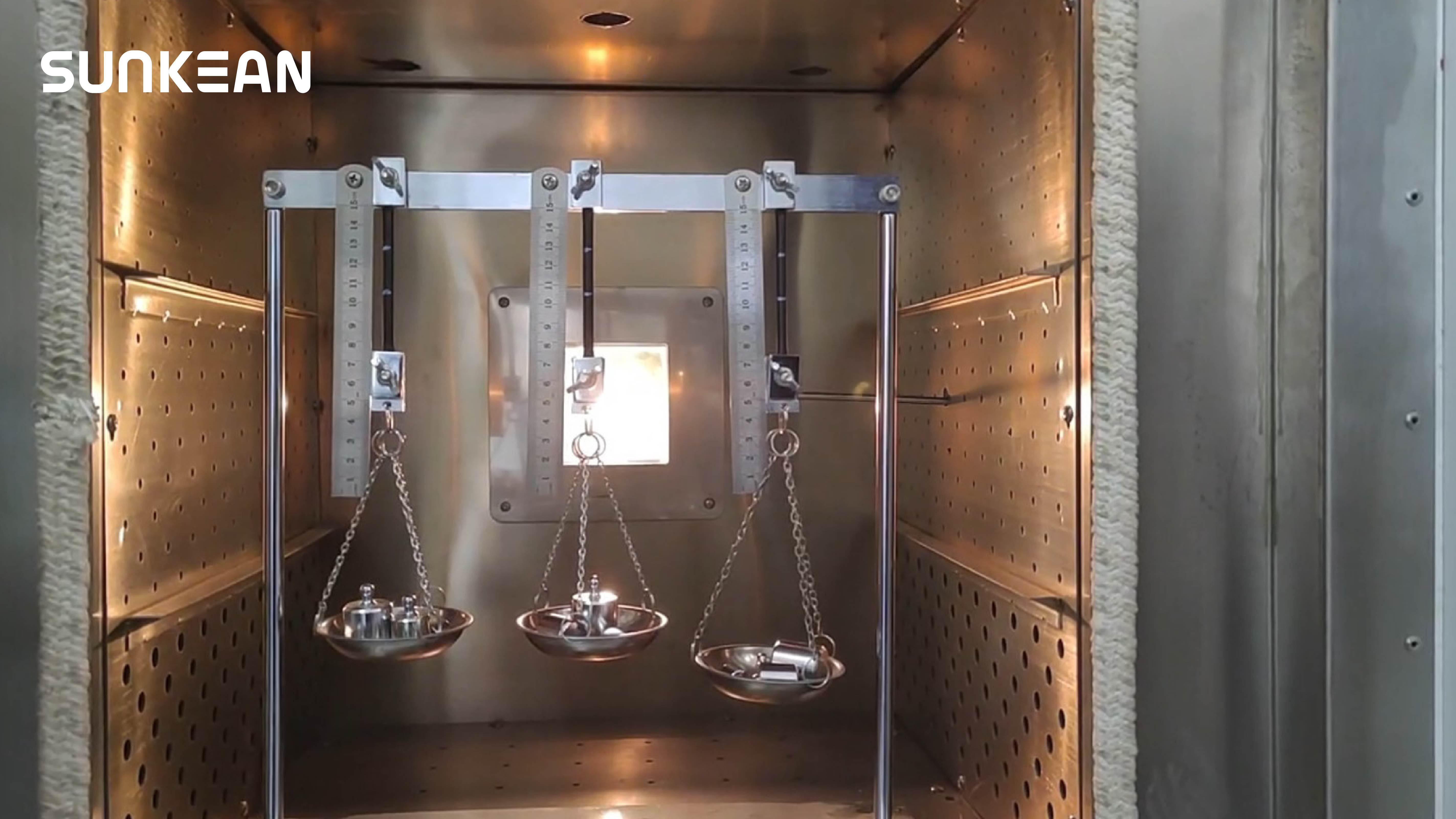
Industry Standards for Solar Cable Tensile Testing
To ensure safety, consistency, and long-term reliability, solar cables must meet stringent mechanical and electrical standards set by authoritative bodies like IEC (International Electrotechnical Commission), UL (Underwriters Laboratories), and TÜV (Technischer Überwachungsverein). Tensile strength is a core evaluation metric within these standards.
IEC 62930: This globally recognized standard specifies the design, construction, and testing requirements for single-core and multi-core flexible cables used in PV systems. It clearly defines specific numerical requirements for the tensile strength and elongation at break of both conductors and insulation. Cables certified to IEC prove their ability to withstand installation and operational stresses.
EN 50618 (H1Z2Z2-K): This European solar cable standard also incorporates tensile testing into its mechanical performance requirements. It specifies minimum tensile strength and elongation values for insulation and sheath materials, which must be met even after accelerated aging tests like UV exposure, thermal cycling, and ozone resistance. Compliance with EN 50618 ensures cables are suited to Europe's diverse climates.
UL 4703: The core standard for the North American market, covering requirements for PV wire, includes tensile testing of insulation and jacket materials to evaluate mechanical durability, ensuring cables resist cracking or failure during field use.
Third-Party Certification (e.g., TÜV): Many solar cables also undergo testing and certification by independent laboratories like TÜV Rheinland or TÜV SÜD. These bodies typically base their tests on IEC or EN standards and may add stricter testing protocols. TÜV certification is a globally recognized mark of product safety and reliability.
How Materials and Construction Impact Solar Cable Tensile Performance?
Conductor Material to Solar Cable Tensile
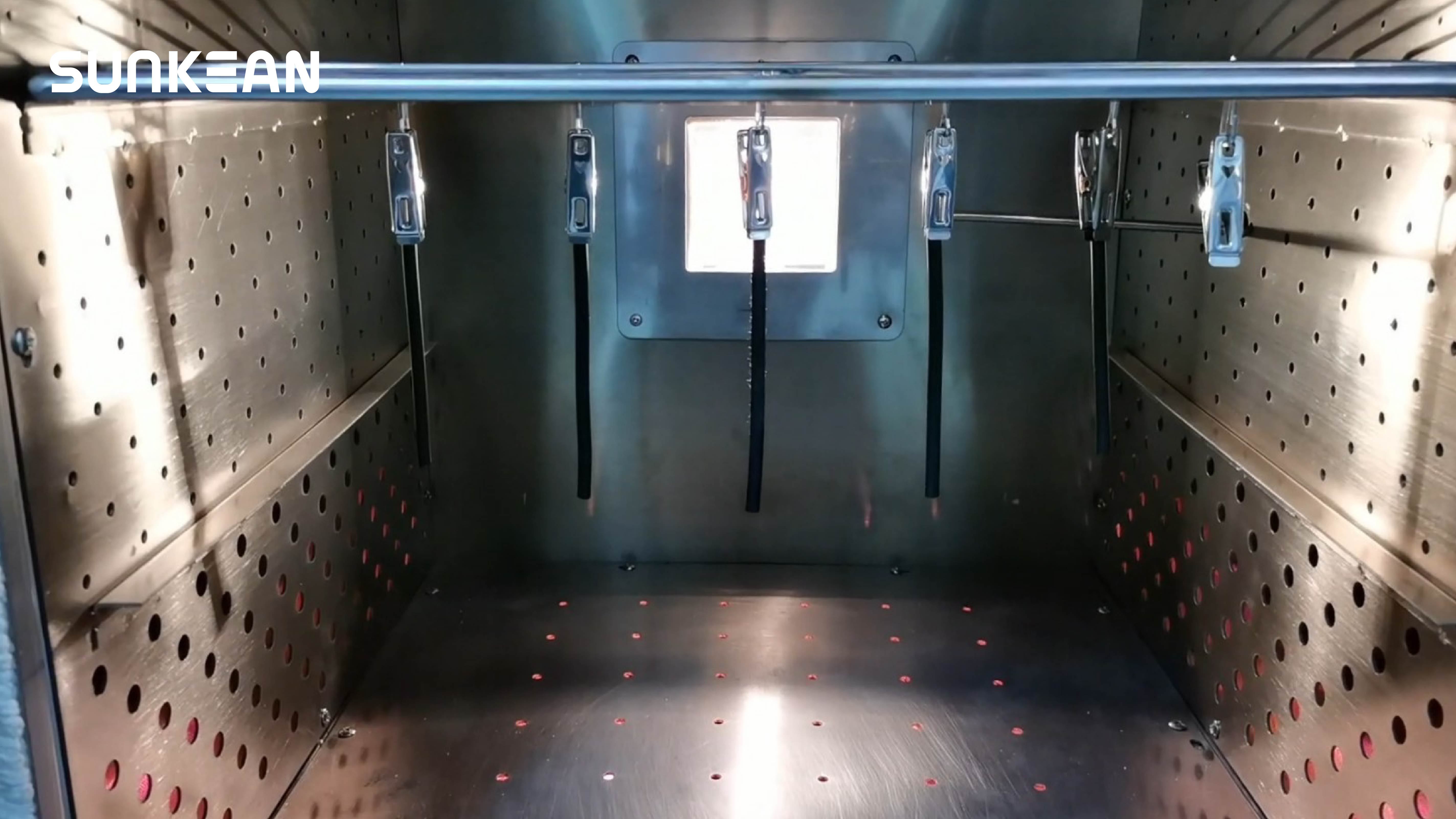
Copper Conductor: The most common choice, offering excellent conductivity, tensile strength, and flexibility (high elongation at break). Tinned copper enhances corrosion resistance. A finely stranded structure further improves flexibility and resistance to bending/tensile fatigue.
Aluminum Conductor: Lightweight and economical, but has lower tensile strength and is more prone to fatigue elongation. Often requires a larger cross-section or reinforced insulation/jacket to meet requirements, commonly used for long-distance runs in large power plants.
Insulation and Sheath Materials to Solar Cable Tensile
The outer materials (typically cross-linked polymers) protect the conductor and ensure overall durability. Their tensile strength and elongation at break are critical, effectively preventing insulation cracking during pulling, withstanding thermal expansion/contraction, and maintaining flexibility under extreme temperatures. Standards like IEC 62930 and EN 50618 require materials to maintain minimum tensile performance even after artificial accelerated aging (UV, heat, ozone), guaranteeing decades of outdoor service life.
Criticality of Manufacturing Processes to Solar Cable Tensile
Conductor Stranding: Tight, uniform fine stranding optimizes flexibility, distributes stress, reduces the risk of individual strand breakage, and enhances resistance to sudden pulls and long-term dynamic loads (wind, thermal expansion, vibration).
Insulation Bonding: Strong adhesion between the conductor and insulation is crucial to prevent the insulation from slipping, separating, or "necking down" (localized thinning) under stress, enhancing overall structural stability.
Material Cross-Linking: Strengthening the molecular structure via chemical or irradiation methods significantly boosts tensile strength, elongation at break, heat resistance, and resistance to aging (UV, high temperatures, abrasion). This is the core process guaranteeing a 25-year service life.
How Do Manufacturers Ensure Solar Cable Tensile Strength?
To ensure solar cables possess qualified tensile strength, manufacturers implement comprehensive measures: They strictly screen raw materials, selecting high-purity annealed copper or quality aluminum for conductors, and use cross-linked polymers compliant with or exceeding standards like IEC 62930/EN 50618 for insulation and sheathing to ensure strength and durability.
During manufacturing, they optimize conductor structure using precision stranding equipment, precisely control insulation/sheath extrusion thickness and bonding strength, and strictly implement chemical or irradiation cross-linking processes to reinforce the material's molecular structure.
Simultaneously, online sensors monitor key parameters in real-time to ensure process consistency. Every production batch undergoes standardized tensile testing in the laboratory, covering both the conductor and sheath materials, with tests for maximum tensile force, elongation at break, etc., conducted under normal conditions and after accelerated aging.
Furthermore, they strictly adhere to international standards like IEC 62930 and UL 4703 throughout the design and production process. Products are submitted to authoritative bodies like TÜV and UL for independent testing and certification, complemented by regular factory audits to ensure ongoing compliance and secure market access qualifications.
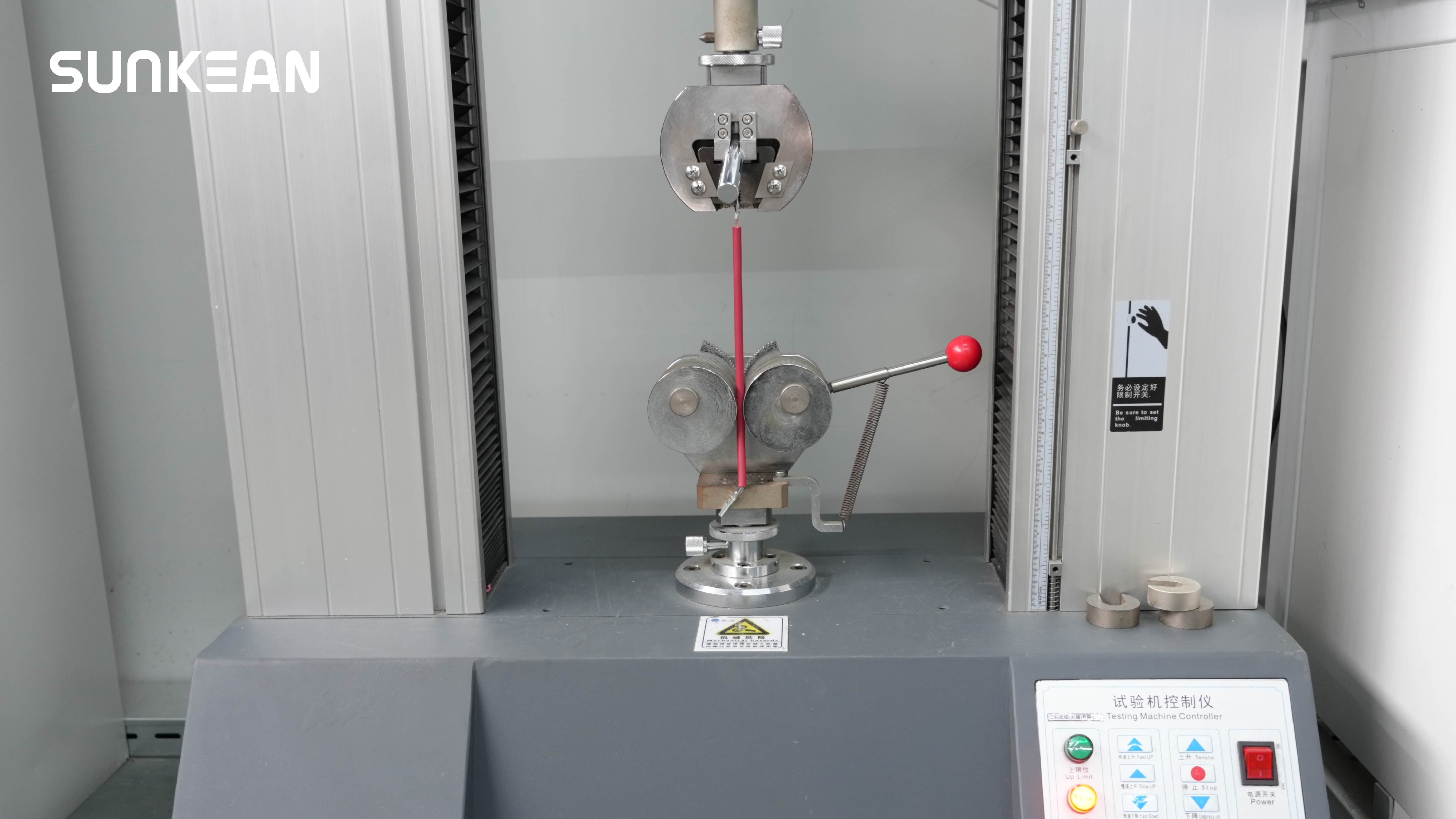